Heat exchangers in heat pump systems transfer heat between refrigerants and air or water, essential for efficient heating and cooling. Common types include plate, shell-and-tube, and finned-tube designs, each suited for specific applications. They often use flow configurations like counterflow and crossflow to maximize efficiency. Innovations in materials and manufacturing boost performance and durability. To understand how these components work together and improve system efficiency, explore further details below.
Key Takeaways
- Heat exchangers transfer heat between refrigerant and air or water, essential for system efficiency.
- Common types include plate, shell-and-tube, coil-in-plate, finned-tube, and air-cooled exchangers.
- They operate in heating mode (extracting outside heat) and cooling mode (removing indoor heat).
- Flow configurations like counterflow and parallel flow optimize heat transfer effectiveness.
- Material choice and design innovations enhance durability, thermal performance, and system reliability.
Understanding Heat Exchangers in Heat Pump Systems
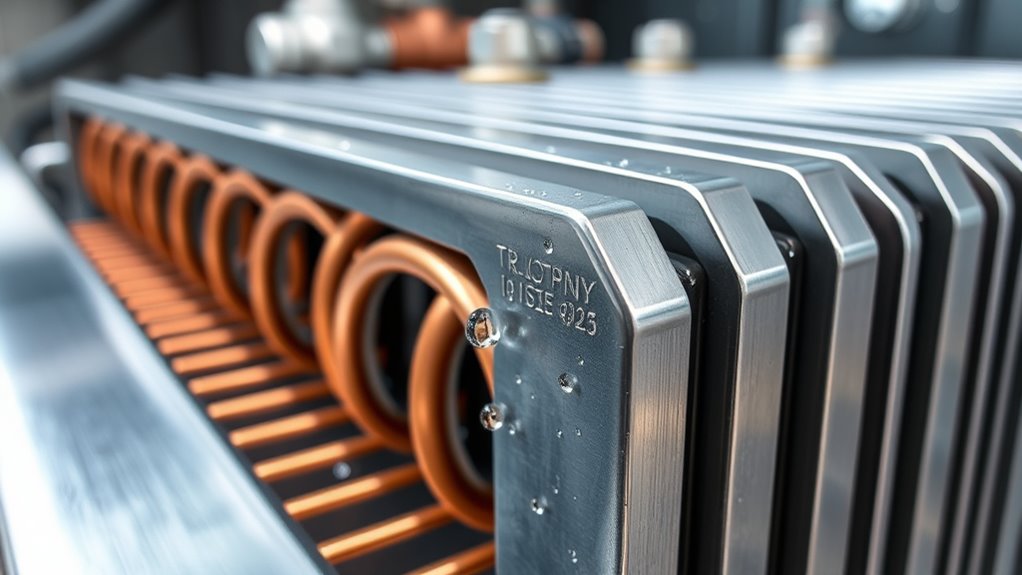
Heat exchangers are essential components in heat pump systems because they facilitate the transfer of heat between the refrigerant and the surrounding air or water. In these systems, heat transfer occurs through various types of heat exchangers, such as plate heat exchangers, shell-and-tube designs, or coil-in-plate configurations. These designs maximize surface area, improving efficiency and thermal energy transfer. The flow configuration, whether counterflow or parallel flow, also influences performance. In heating mode, heat exchangers extract thermal energy from outside air or water and transfer it indoors; in cooling mode, they remove heat from indoor air. The choice of heat exchanger type impacts the energy system’s overall efficiency and reliability, making them crucial for optimal heat pump operation. Additionally, selecting the appropriate heat exchanger involves considering space and organization, as efficient layouts can facilitate maintenance and upgrades, and choosing materials compatible with operating conditions enhances durability. Furthermore, understanding the environmental conditions where the system operates can help optimize heat exchanger performance and longevity.
Core Principles of Heat Transfer in Heat Pumps
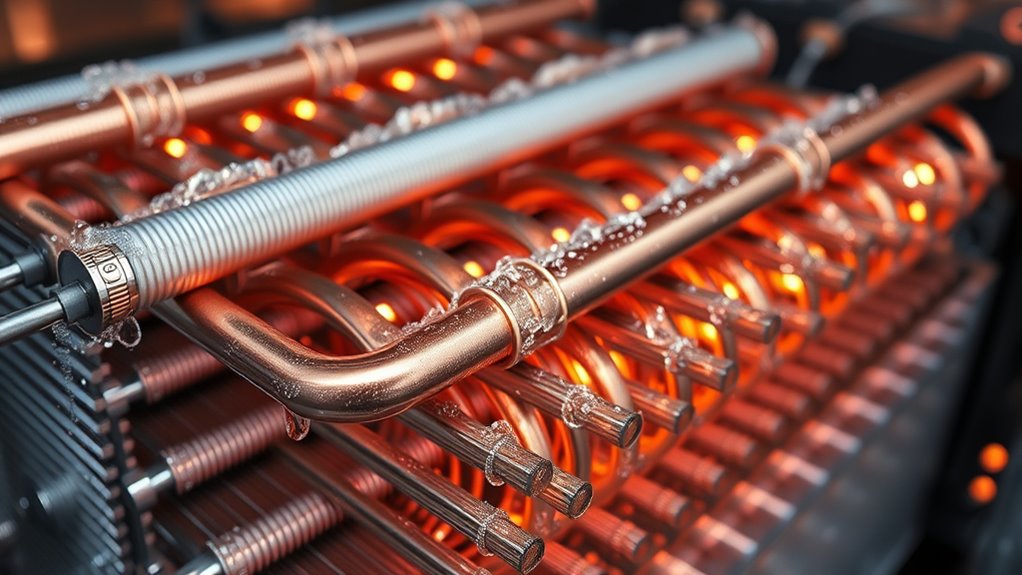
Understanding how heat moves in a heat pump is essential to optimizing its performance. You rely on conduction, convection, and radiation to transfer heat effectively between components. By grasping these mechanisms and their thermodynamic principles, you’ll better appreciate how temperature differences and system design influence efficiency. Additionally, the color accuracy of the system’s components can impact overall performance and reliability. Recognizing the importance of heat transfer mechanisms helps in diagnosing issues and improving system design for better energy efficiency. Moreover, an understanding of system operating hours can assist in maintenance planning and performance assessment. Being aware of material properties, such as thermal conductivity, further enhances the ability to optimize heat transfer within the system.
Heat Transfer Mechanisms
In heat pump systems, transferring thermal energy relies on three primary mechanisms: conduction through solid components, convection within fluids, and thermal radiation. Conduction occurs when heat moves through materials with high thermal conductivity, driven by a temperature gradient and quantified by the heat transfer coefficient. Convection involves fluid motion transferring heat with the surface, depending on the heat transfer coefficient, surface area, and temperature difference. Thermal radiation, following the Stefan-Boltzmann Law, increases with temperature and surface emissivity. To optimize heat transfer, you should maximize surface area, select materials with high thermal conductivity, and enhance temperature gradients. Understanding these mechanisms helps improve heat exchanger efficiency, ensuring effective heat movement in your heat pump system. Additionally, selecting appropriate materials can significantly enhance conduction efficiency due to their superior thermal properties. Furthermore, employing advanced surface treatments can improve the heat transfer performance by reducing thermal resistance at interfaces.
Thermodynamic Principles
Thermodynamic principles form the foundation for how heat transfer occurs within heat pump systems. You rely on conduction, convection, and radiation to transfer heat efficiently. Fourier’s Law describes how conduction depends on the temperature gradient and material properties, while Newton’s Law of Cooling explains convection’s heat transfer rate based on surface temperature differences. The Stefan-Boltzmann Law governs radiative heat exchange, especially at higher temperatures. These processes work within a thermodynamic cycle, involving phase changes of refrigerants—absorbing heat during evaporation and releasing it during condensation—driven by work from a compressor. The coefficient of performance (COP) measures system efficiency, indicating how effectively heat is transferred relative to energy input. These principles ensure heat moves from a source to a sink, enabling effective heat pump operation.
Common Types of Heat Exchangers Used in Heat Pumps
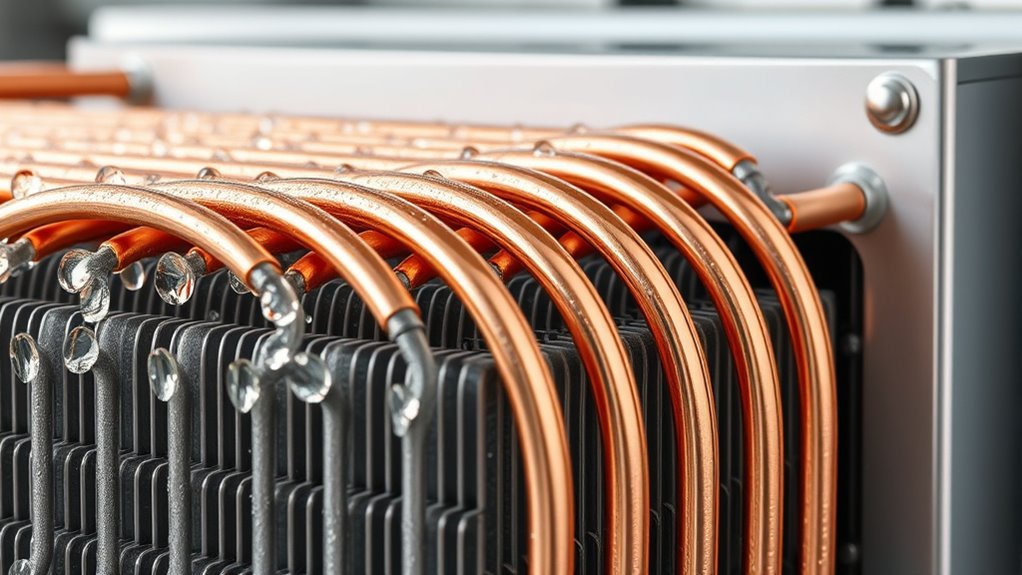
Various types of heat exchangers are integral to heat pump systems, each chosen for specific performance needs and operating conditions. For high heat transfer efficiency and compact design, you might use plate heat exchangers, which feature stacked metal plates that promote turbulence. Shell and tube heat exchangers are ideal for large-scale systems, thanks to their durability, ease of maintenance, and ability to handle high-pressure refrigerants. Finned-tube heat exchangers boost surface area with fins, improving heat transfer in air-to-refrigerant or refrigerant-to-air processes. Other options include air-cooled heat exchangers, which dissipate heat directly into the air using fans, and spiral heat exchangers, suited for viscous or fouling-prone fluids. These heat exchangers types are essential components of heat pump systems and HVAC applications, fulfilling various heat exchanger functions.
How Countercurrent and Cross Flow Configurations Work
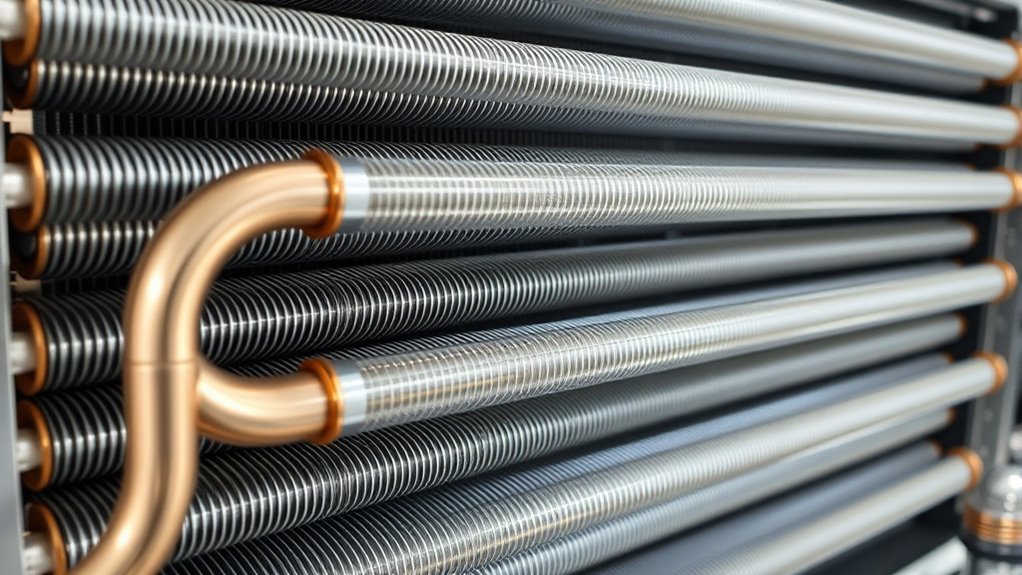
Understanding how fluids flow within heat exchangers helps optimize their performance in heat pump systems. In a countercurrent flow, fluids move in opposite directions, maximizing the temperature difference and boosting heat transfer efficiency. Cross flow configurations have fluids moving perpendicular to each other, offering moderate efficiency suitable for gases or vapor. These flow arrangements influence heat exchanger design and thermal performance, with countercurrent setups often nearing maximum heat exchange effectiveness. Cross flow systems, being more compact, suit space-constrained applications. Your choice depends on factors like desired efficiency, fluid properties, and space. Here’s a comparison:
Flow Type | Fluid Movement | Key Benefit |
---|---|---|
Countercurrent | Opposite directions | Higher thermal performance |
Cross Flow | Perpendicular flow | Space-efficient, flexible |
Efficiency | Maximize heat transfer | Optimize system performance |
Additionally, selecting the appropriate flow type can impact the overall heat transfer efficiency of the system, which is crucial for optimal operation.
Material Innovations Enhancing Heat Exchanger Performance
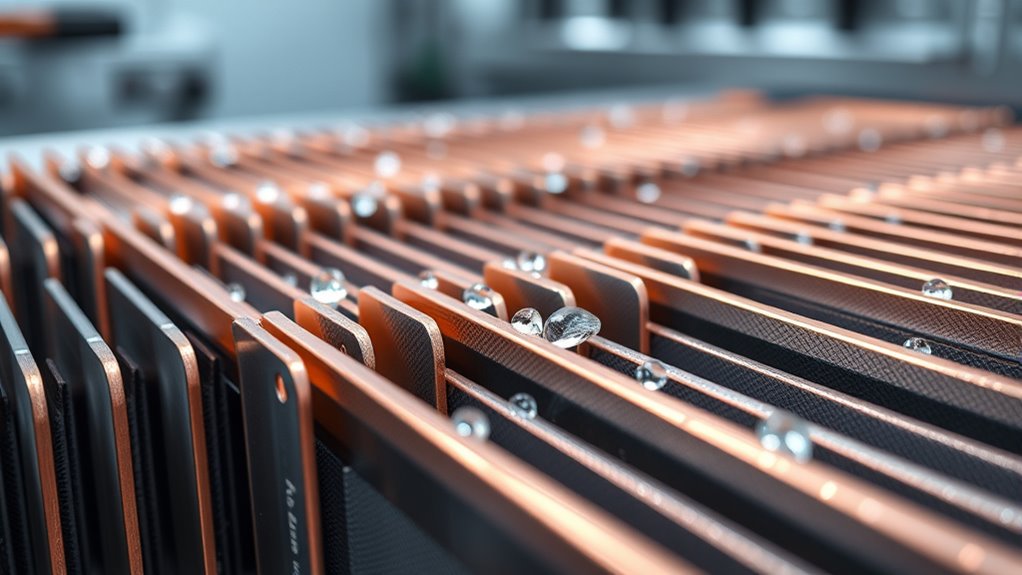
Recent advances in material science have considerably boosted heat exchanger performance by introducing high-conductivity and corrosion-resistant materials. Graphene and nanostructured composites substantially enhance thermal conductivity, enabling faster heat transfer. Corrosion-resistant alloys like titanium and specialized coatings extend lifespan in harsh environments. Innovations with lightweight, high-strength alloys and composites reduce system weight and improve efficiency. Incorporating phase change materials (PCMs) boosts thermal storage, optimizing heat pump operation. Additive manufacturing allows for complex geometries that maximize surface area and flow characteristics. Additionally, headphone connector advancements in connector and wireless technology improve system integration and user convenience. These material innovations collectively elevate heat exchanger performance by improving durability, thermal efficiency, and design flexibility. The development of advanced manufacturing techniques allows for the creation of more intricate and optimized heat exchanger designs, further enhancing their effectiveness. Furthermore, ongoing research into thermal management materials is pivotal in developing heat exchangers capable of operating under increasingly demanding conditions, ensuring longevity and reliability. For example, the integration of smart materials enables adaptive thermal management, further optimizing heat transfer efficiency. You benefit from longer-lasting, more efficient systems that perform better under demanding conditions, thanks to these cutting-edge materials shaping the future of heat pump technology.
Role of Advanced Manufacturing Techniques in Heat Exchanger Design
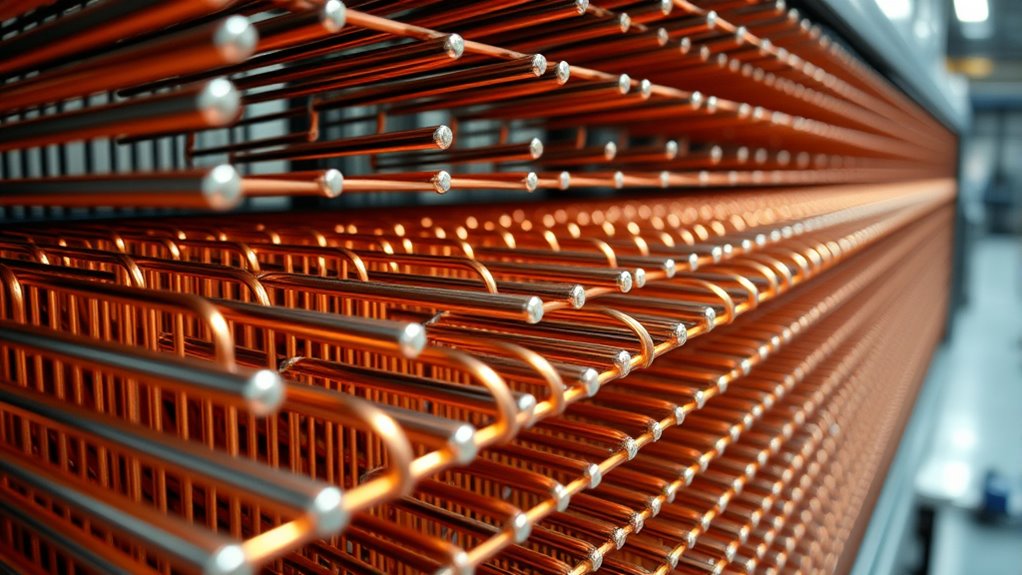
Advanced manufacturing techniques, particularly 3D printing, are transforming heat exchanger design by enabling the creation of complex, lightweight structures with optimized geometries. Additive manufacturing allows for rapid prototyping and customization, so you can tailor heat exchangers to specific heat transfer needs and spatial constraints. Material deposition methods enhance durability and thermal conductivity, boosting efficiency and lifespan. With design optimization powered by AI, you can develop innovative structures that maximize surface area and heat transfer rates. These advanced manufacturing techniques also reduce production costs and lead times, making it easier to implement cutting-edge designs in heat pump systems. Overall, additive manufacturing broadens your options for creating high-performance, efficient heat exchangers with complex geometries that were previously difficult or impossible to produce. Diverse designs available to enhance heat exchanger performance further expand your possibilities for innovation. Moreover, the use of advanced materials can further improve thermal performance and corrosion resistance in these innovative structures. Additionally, incorporating manufacturing flexibility allows for more intricate and tailored heat exchanger configurations that optimize system performance. Furthermore, the integration of design optimization tools accelerates the development process, ensuring that the final product meets specific operational requirements efficiently. The implementation of vetted manufacturing techniques also ensures reliability and quality in the production of these advanced heat exchangers.
Safety and Maintenance Considerations for Heat Exchangers
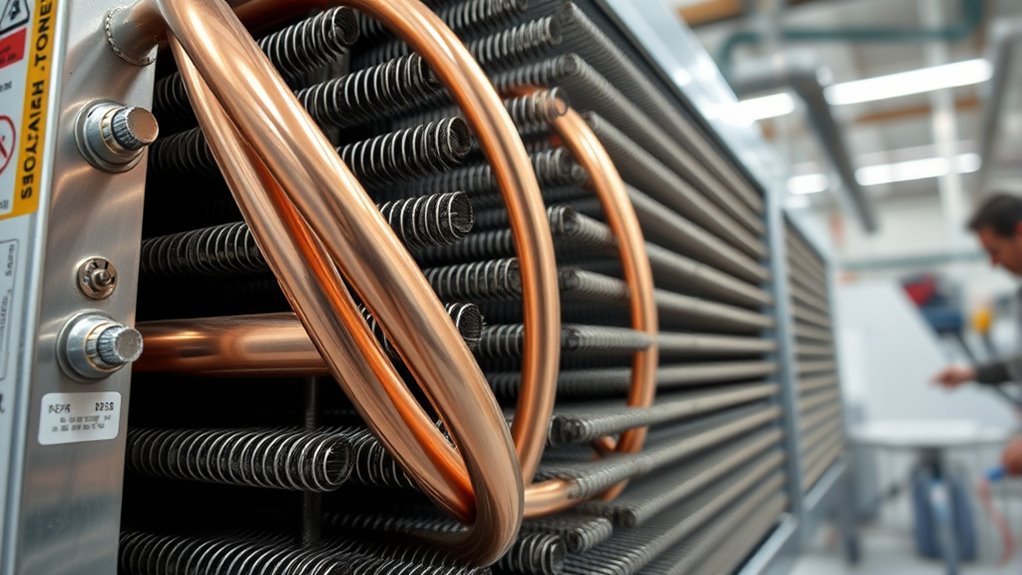
Regular inspections for leaks, corrosion, and cracks are essential to guarantee your heat exchanger operates safely and efficiently. Proper cleaning and filter replacement prevent fouling and corrosion that can lead to hazards. Staying vigilant for unusual noises or CO levels helps catch issues early before they become serious. Incorporating knowledge of heat exchanger maintenance can further extend the lifespan and safety of your system. Additionally, monitoring air quality indicators can help identify potential problems with emissions or system performance. Using crochet kits for beginners can also be useful in customizing protective covers or labels for maintenance accessories to ensure safety protocols are followed.
Inspection and Leak Detection
How can you effectively detect leaks in heat exchangers to guarantee safety and proper maintenance? Start by monitoring ambient CO levels; a rise above zero suggests potential gas leaks or cracks. Conduct flame displacement tests to check flame stability; fluctuations or extinguishments indicate leaks. Use combustion analysis to measure CO and other emissions—elevated levels confirm leaks or cracks. Regular visual inspections help identify early signs of corrosion, cracks, or discoloration that may compromise structural integrity. For more thorough detection, employ ultrasonic testing or dye penetrant methods periodically. These non-destructive techniques reveal hidden flaws and confirm the exchanger’s safety. Incorporating innovative testing techniques such as acoustic emission monitoring can further enhance early leak detection and prevent costly failures. Additionally, AI-driven diagnostics can analyze data more accurately and promptly identify potential issues before they become critical. Proper maintenance protocols also include routine cleaning to prevent buildup that could mask leaks or cause corrosion. Staying vigilant through continuous monitoring can help catch issues early, reducing downtime and maintenance costs. Implementing regular testing schedules ensures ongoing safety and operational efficiency.
Proper Cleaning Procedures
To guarantee safe and effective cleaning of heat exchangers, you must follow proper procedures that prioritize safety and maintenance. Begin with routine inspection to identify fouling, corrosion, or leaks, which can impair system performance. Choose appropriate cleaning procedures, such as chemical descaling for mineral buildup or mechanical brushing for surface fouling, based on the material and type of fouling. Always adhere to safety guidelines, disconnect power sources, and wear personal protective equipment like gloves, goggles, and respirators to prevent chemical exposure or debris inhalation. Proper cleaning not only restores efficiency but also prevents damage from corrosion. Regular maintenance, combined with professional inspections, helps catch early signs of deterioration, ensuring the heat exchanger operates safely and efficiently over time.
Diagnosing and Addressing Common Heat Exchanger Issues
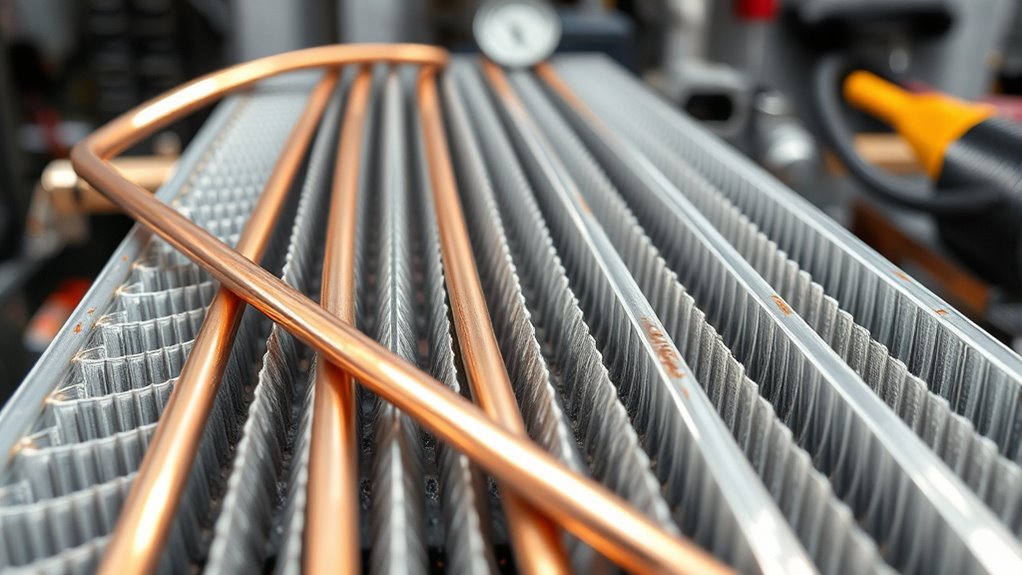
Diagnosing common heat exchanger issues involves systematic inspection and testing to detect damage early. Elevated ambient CO levels can indicate cracks or leaks, so monitoring these levels is vital. Conduct flame displacement tests to observe flame stability; fluctuations or extinguishments suggest leaks. Regular inspection helps identify corrosion, buildup, or physical damage that compromise safety and efficiency. Performing combustion analysis to measure CO and other gases can reveal crack-induced leaks, guiding necessary repairs. Addressing issues promptly prevents further damage and maintains ideal performance. Remember, proper maintenance, including timely repair or replacement of cracked or severely damaged units, ensures safety, reduces emissions, and sustains system efficiency. Consistent damage detection and proactive maintenance are key to long-term heat exchanger health.
Future Trends and Technologies in Heat Exchanger Development
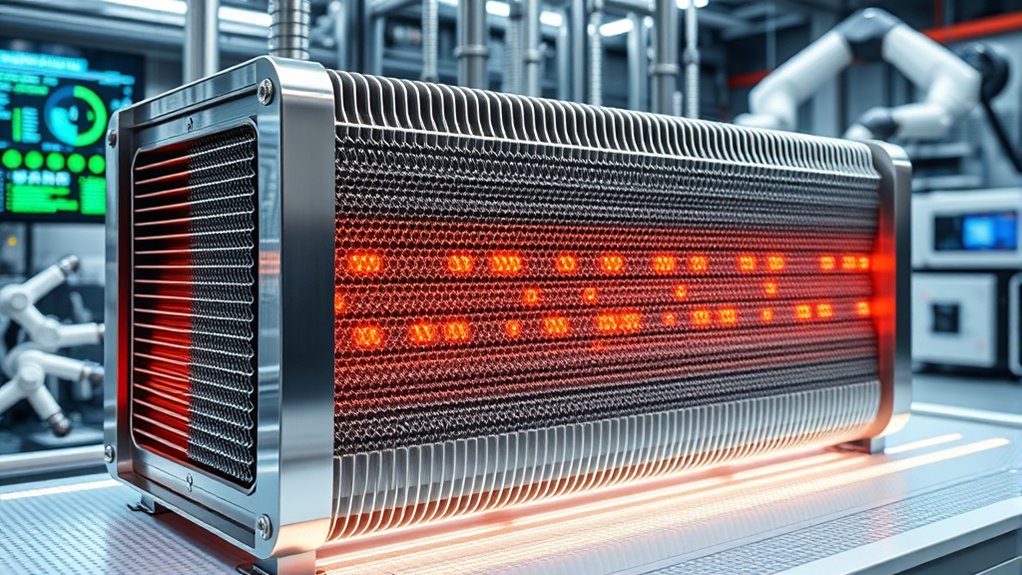
Advancements in heat exchanger technology are driving significant improvements in efficiency, durability, and sustainability. You’ll see the rise of nanostructured composites and high-thermal-conductivity alloys that boost heat transfer and extend lifespan. AI optimization plays a key role, enabling real-time performance tuning, predictive maintenance, and adaptive control. Additive manufacturing allows for complex, lightweight, and customized components, enhancing thermal performance while reducing size. Emerging designs incorporate phase-change materials and innovative flow configurations to maximize thermal storage and heat transfer rates. Sustainability is prioritized through eco-friendly, corrosion-resistant materials and energy-efficient manufacturing processes. Together, these innovations promise smarter, more efficient heat exchangers that meet future energy and environmental demands while improving system reliability and performance.
Selecting the Right Heat Exchanger for Heat Pump Applications
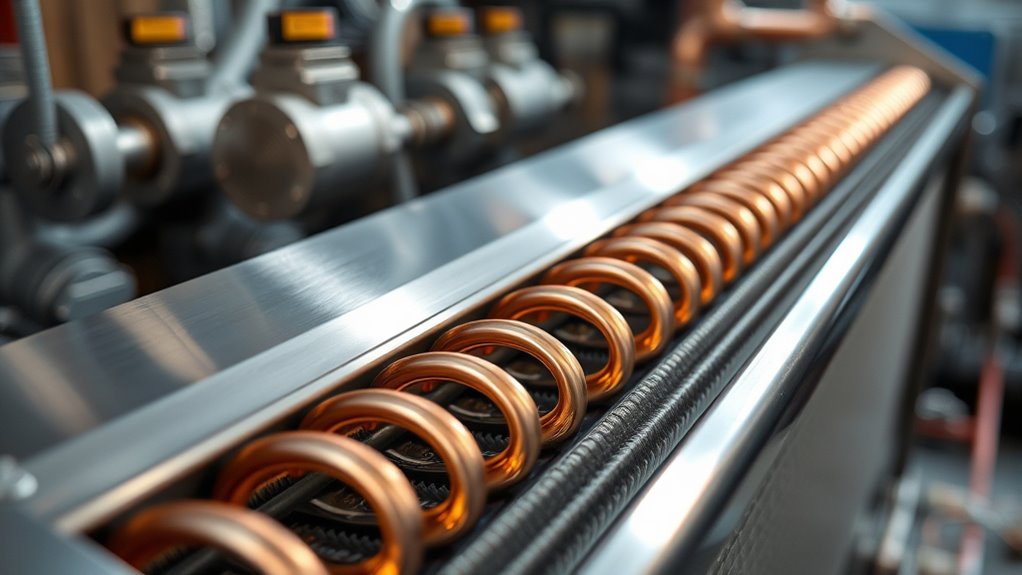
Choosing the right heat exchanger for a heat pump system depends on balancing efficiency, durability, and environmental conditions. Your goal is to optimize thermal transfer efficiency while ensuring longevity. For high heat transfer, consider plate heat exchangers with their compact design and large surface area. Shell and tube models offer durability for high-pressure applications, while finned-tube types boost performance in air-source heat pumps by increasing surface area. Selecting corrosion-resistant materials like copper or stainless steel enhances lifespan in harsh environments. Proper flow configuration, such as countercurrent flow, maximizes heat transfer.
- Consider surface area and flow configuration to improve thermal transfer efficiency.
- Choose corrosion-resistant materials for durability in various heat pump applications.
- Prioritize compact design for space-efficient heat exchanger selection.
Frequently Asked Questions
What Are the 3 Types of Heat Exchangers?
You want to know the three main types of heat exchangers. First, shell and tube exchangers use tubes inside a shell, perfect for high-pressure, high-temperature applications. Second, plate exchangers stack metal plates to boost heat transfer in a compact design. finally, air-cooled exchangers rely on fans to cool fluids by releasing heat into the air. Each type suits different needs based on capacity, space, and fluid properties.
What Is the Heat Exchanger in a Heat Pump?
Think of the heat exchanger as the heart of your heat pump, pumping thermal energy where it’s needed. It transfers heat between the refrigerant and air or water, either absorbing warmth to heat your space or releasing heat to cool it down. Its design, material, and flow setup determine how efficiently it works, making sure your system runs smoothly and saves energy, just like a well-beating heart keeps you going.
What Is the Function of Heat Exchanger in HVAC System?
You want to understand the function of a heat exchanger in an HVAC system. It transfers thermal energy between the refrigerant and air, either indoors or outdoors, to heat or cool your space. By conducting heat through metal surfaces like copper or aluminum, it helps maintain your indoor temperature efficiently. When working properly, it saves energy and keeps your system running smoothly, but damage or fouling can reduce its effectiveness.
What Is the Difference Between Shell & Tube and Double Pipe Heat Exchanger?
You’re asking about the difference between shell and tube and double pipe heat exchangers. Think of it as comparing a big fish to a small one—you get more capacity and efficiency with shell and tube units, which are modular and handle high pressures. Double pipe exchangers are simpler, cost-effective, and better suited for small-scale tasks. Basically, choose shell and tube for large jobs; double pipe for smaller, straightforward needs.
Conclusion
Understanding the different types and functions of heat exchangers helps you optimize your heat pump system. By choosing the right configuration and materials, you can improve efficiency, safety, and longevity. A common theory suggests that innovative materials and designs will revolutionize heat exchanger performance, and evidence supports this—technological advancements continue to enhance energy savings. Embrace these developments to enjoy a more reliable, eco-friendly heating and cooling experience.